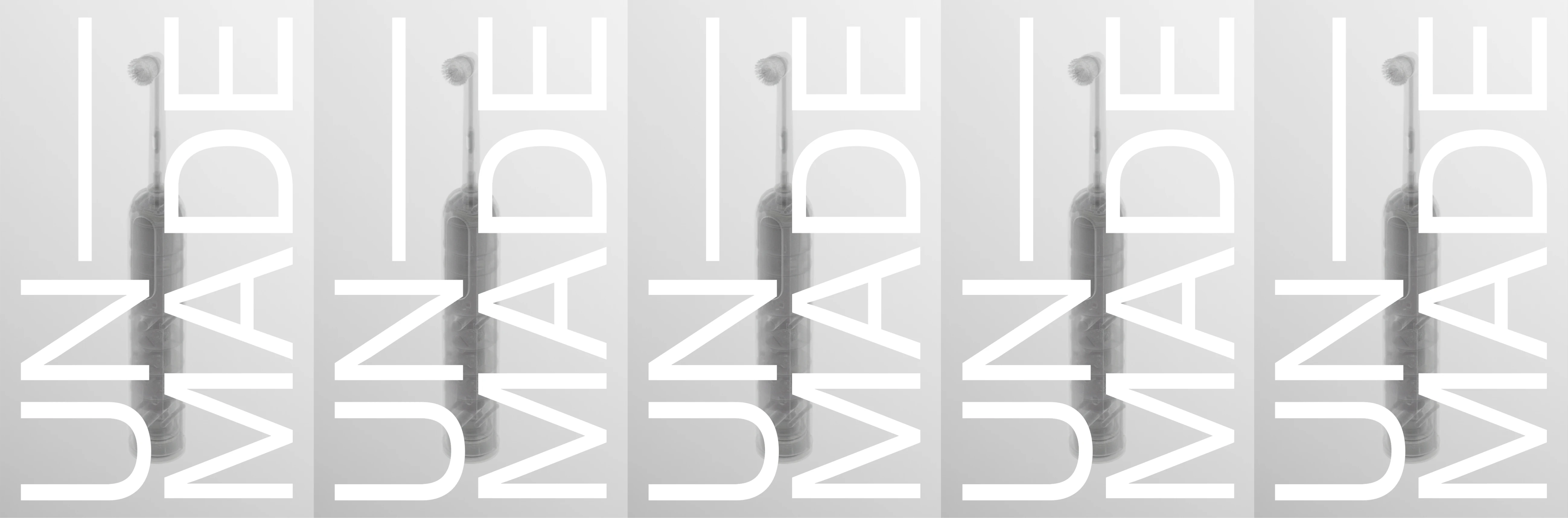
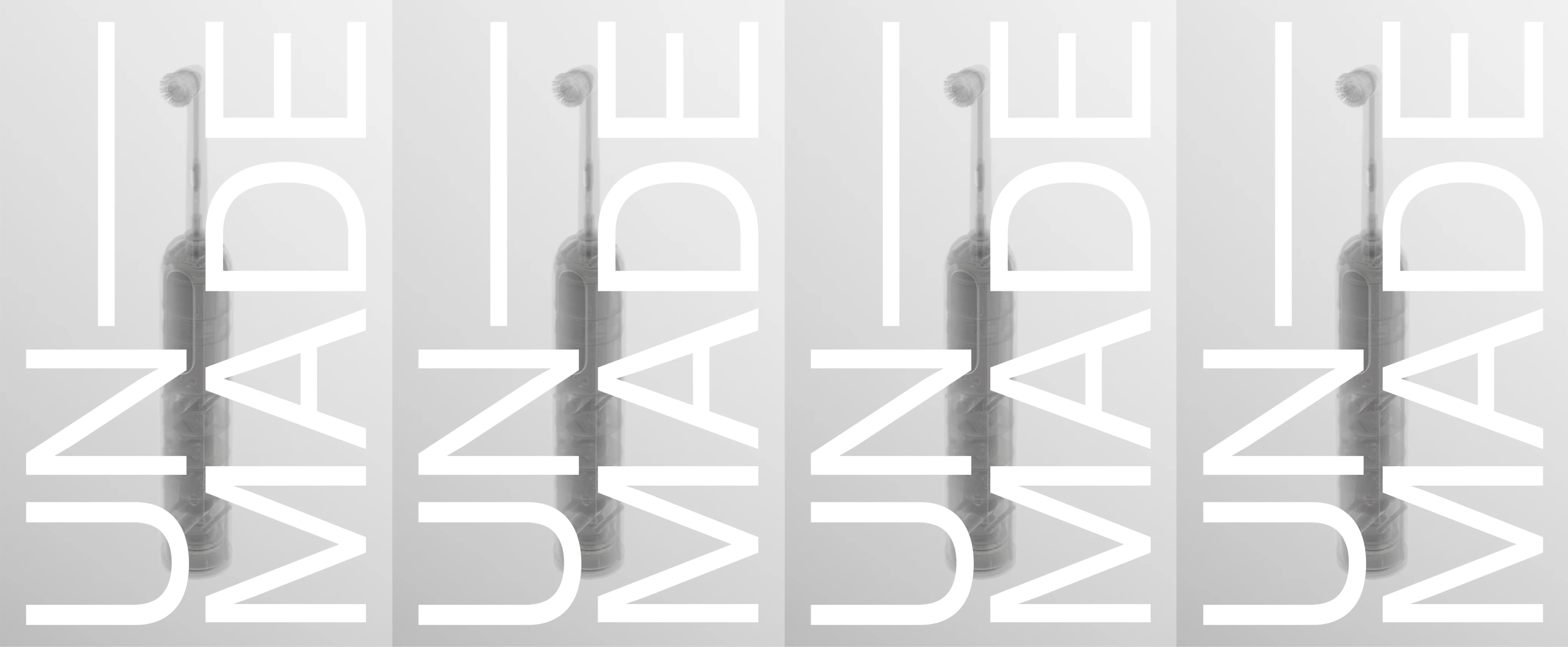
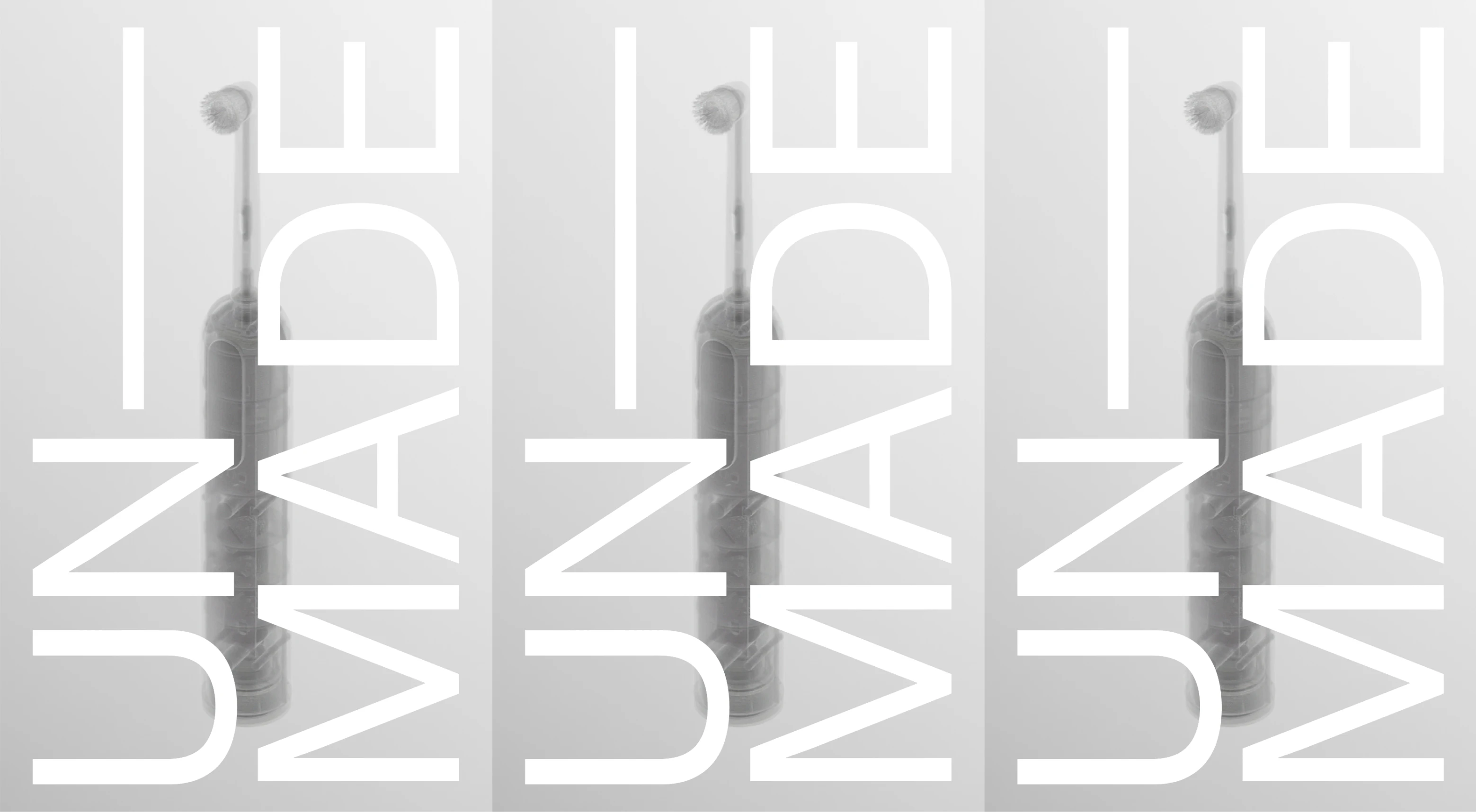
WE NEED TO
RE-THINK
RECYCLING
RECYCLING
RECYCLING
RECYCLING
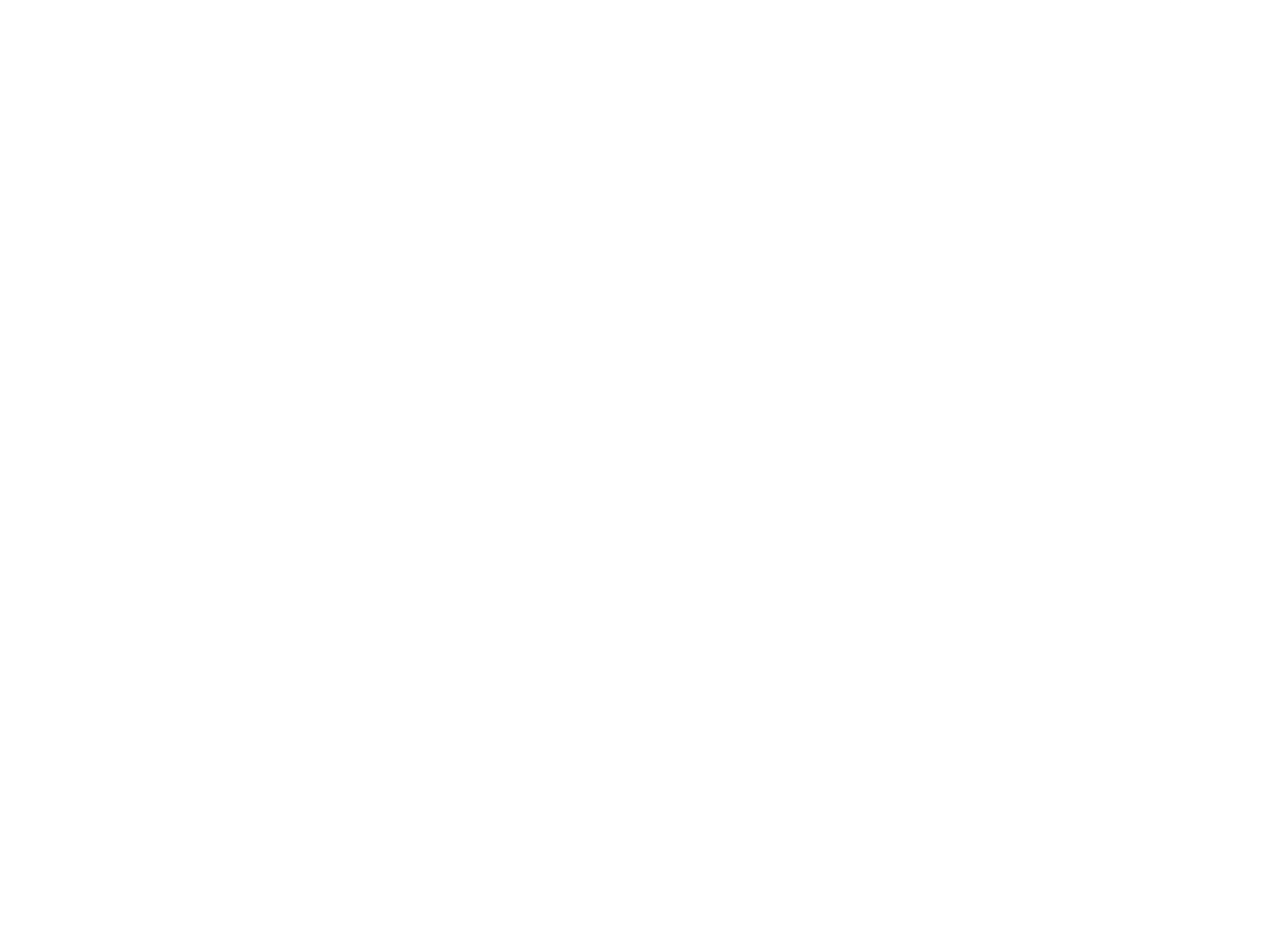
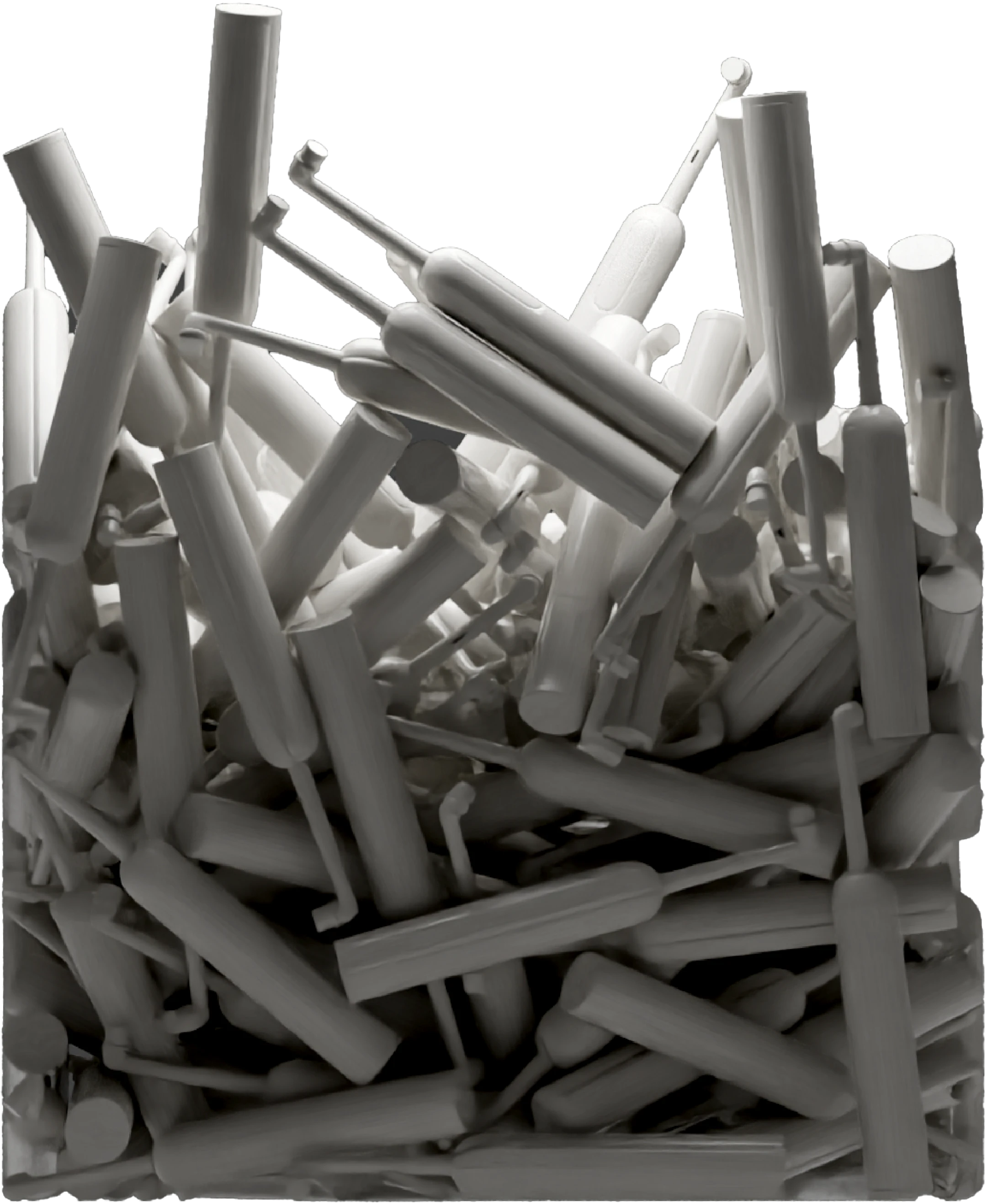
To tackle the rising tide of e-waste from low-cost electronics, we’ve explored automated disassembly mechanisms which make component recovery and recycling more efficient.
The four mechanisms have been applied to an electric toothbrush, but we believe the theory can be applied to other categories.

A project from the Seymourpowell Product Experience team.
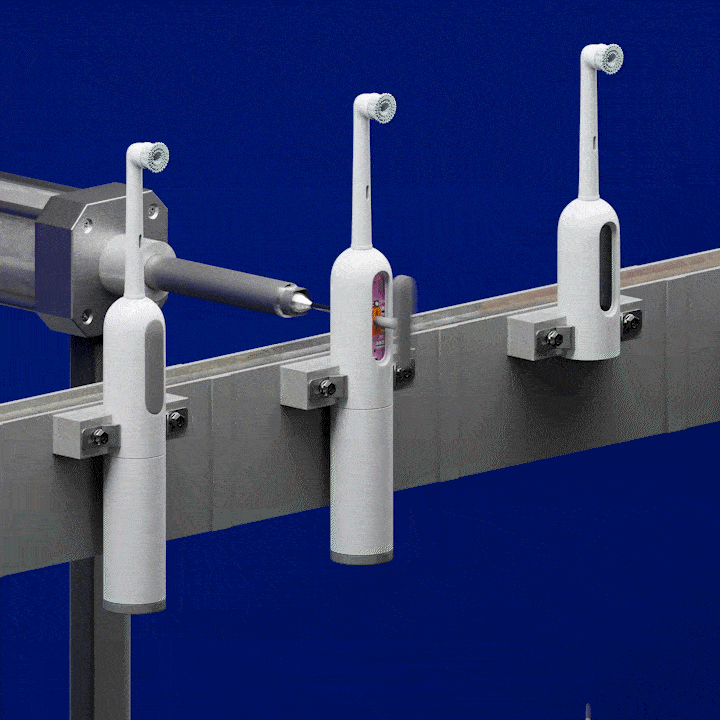
The pin mechanism uses a ‘lynchpin’ style feature which holds the internals and external housing lock in place. A small, sealed pinhole on the rear of the product can be poked, unlocking and ejecting the pin and releasing the internals.
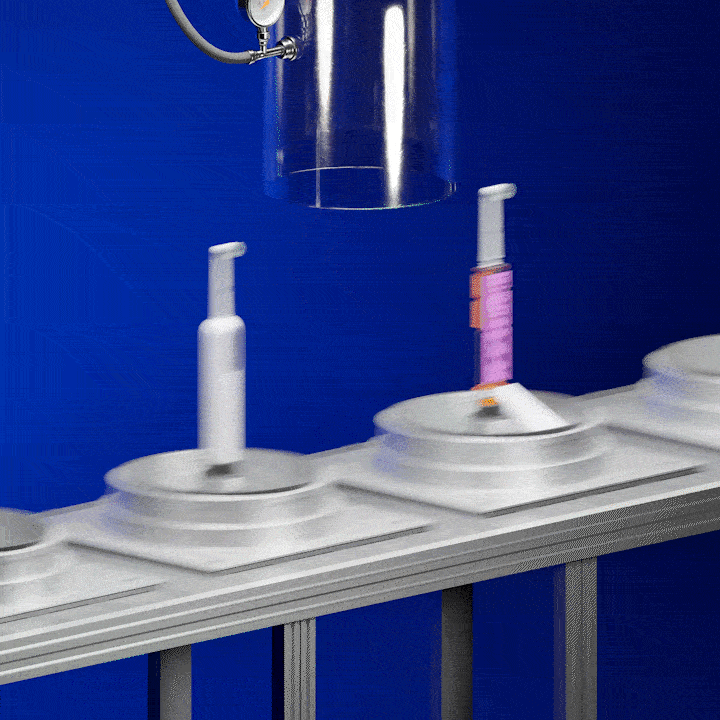
Closed-cell foams and air-sealed features forcefully expand while in a vacuum, splitting the external housing and revealing internal components. This method was inspired by a fantastic student project called ‘The Toaster Project’ ref.
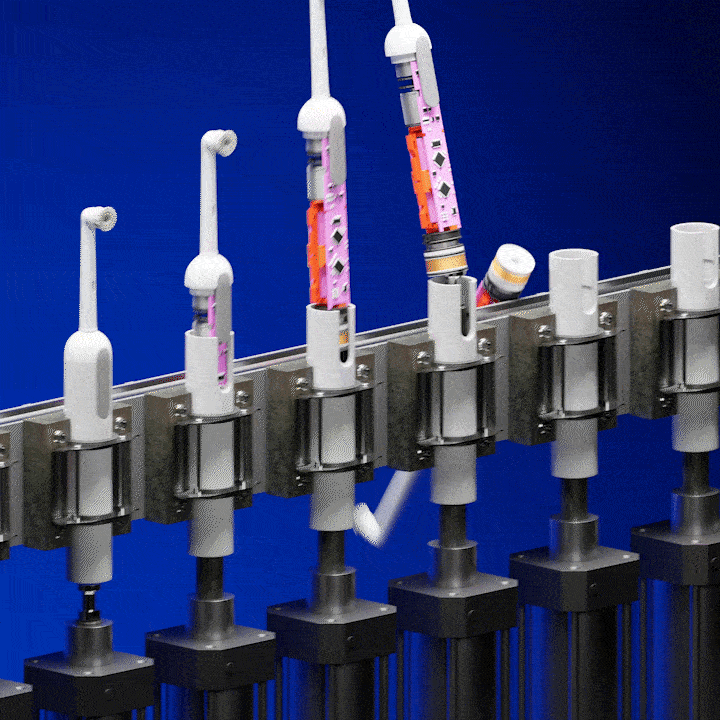
Suitable for extruded constructions, the piston mechanism works by breaking a bottom cap and then pushing all internals out of an extruded housing along the same line of extrusion.
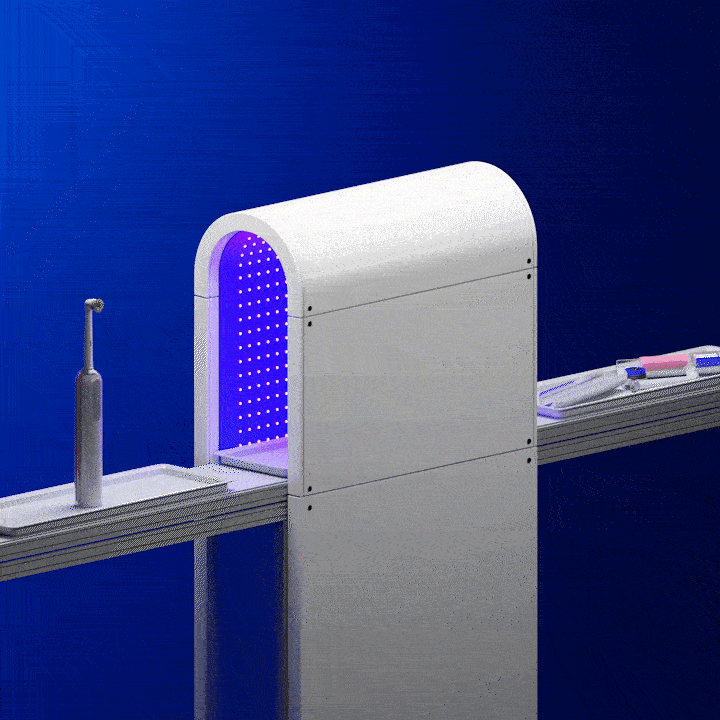
Adhesives running visibly along the seams of the product are deactivated under the presence of ultra-violet light. This releases the clamshell construction and the internals can be easily separated and removed.

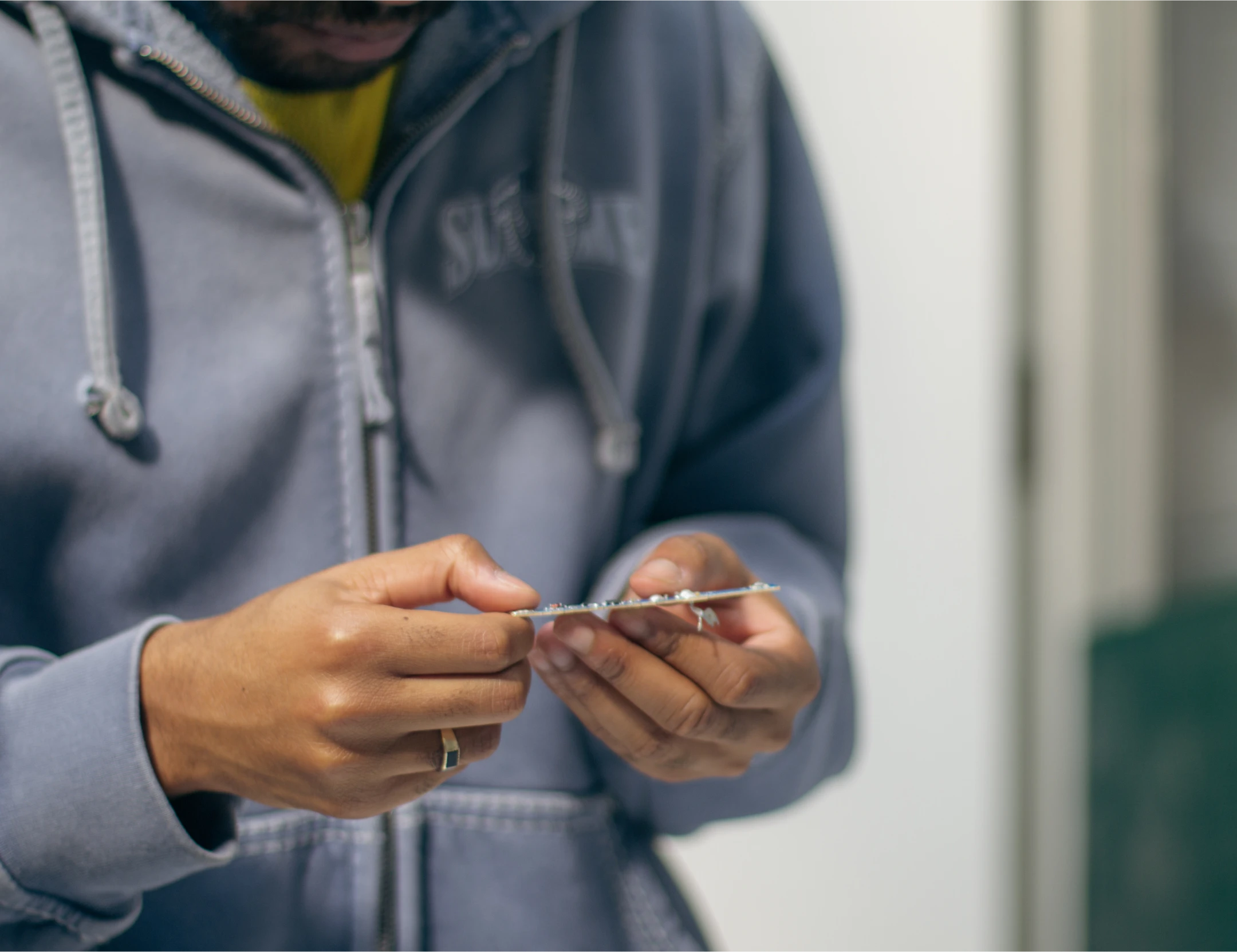
I’m slightly embarrassed to admit it, but I had been manually brushing my teeth for years. That is, until recently, when my dentist recommended an upgrade. I popped online to look through the options.
There was the top-of-the-range model at a rather punchy £400. A ‘sustainable’ choice, with a ‘biodegradable’ PLA brush head, at £75 or the budget option at £24.99. I opted for the cheapest, at which point Amazon smugly pointed out that they’d sold ‘10k+’ of that model last month alone.
As an Industrial Designer, I spend time obsessing over the product I’m working on – typically thinking of it in isolation. But it’s often harder to adequately picture the true scale of its production. 10,000 units is a steep monthly sales figure. What other cheap electronics are selling in these quantities?
According to the Amazon best-sellers list, fabric shavers, steam irons, wireless doorbells, wireless mice, digital tyre inflators and USB-C adaptors are selling in their thousands every month – each costing less than £20 per unit.
The destiny for these cheap electronics? Products will be left behind in hotel bathrooms, batteries will run flat, and the gross toothpaste crust accumulation will become too much, making a one-way trip to the bin likely.
This (despite boosting sales for the likes of Amazon) is a huge issue and a key reason why e-waste is the fastest growing waste stream globally. Cheap electronics could, in theory, last longer but they’re simply not designed to do so.

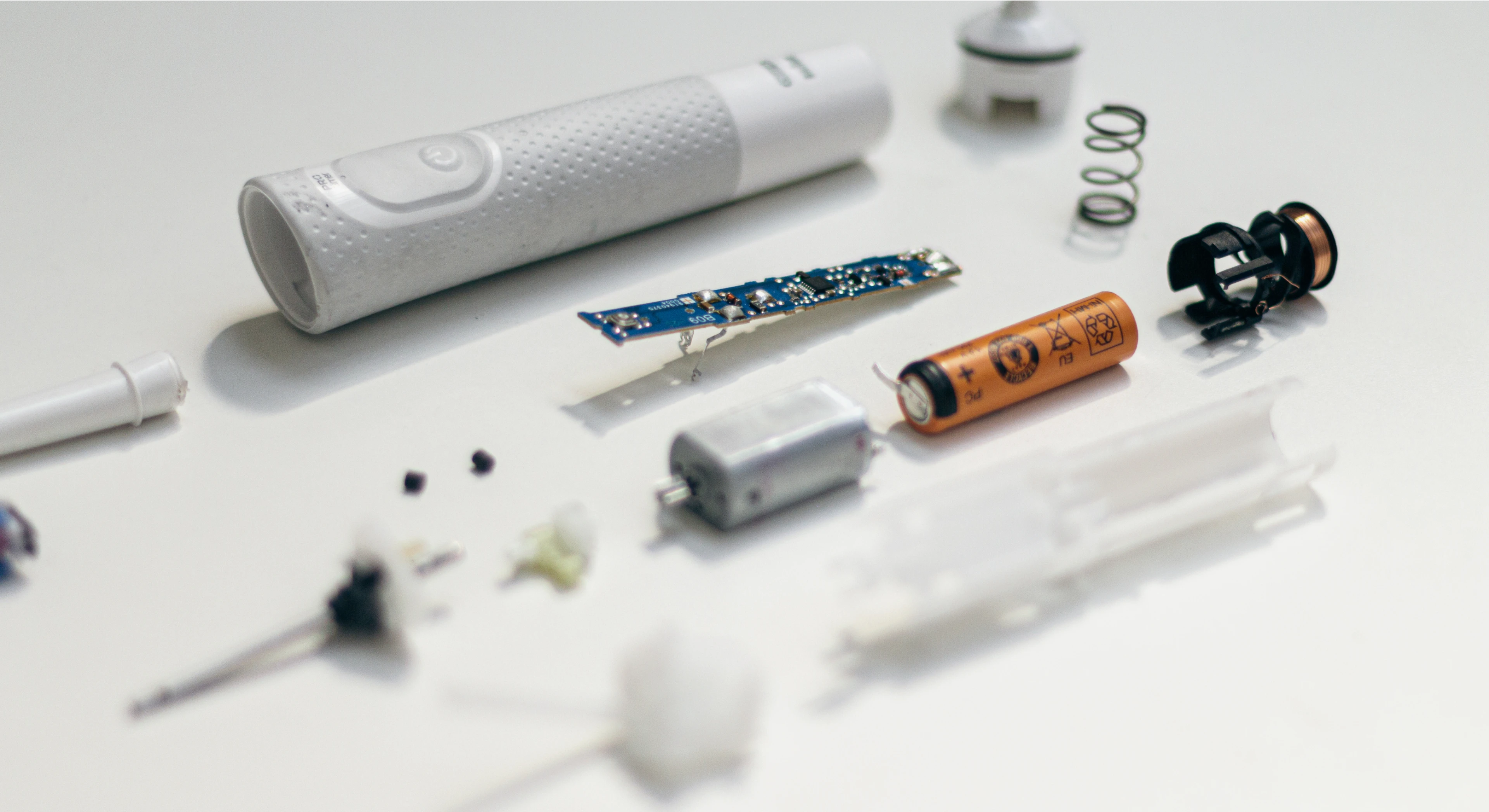
Durable Products: Recycling vs Repair vs Recovery
The challenge is how do we deal with this deluge of cheap, complex electronic goods entering the market? We must aim to create a more circular economy.
Keeping products circulating at their highest value is a key driver of the circular economy. A push for more durable, repairable consumer electronics is taking place within the industrial design sphere.
However, with repair comes a host of technical and societal challenges, typically boiling down to two issues: can we make repairable products for the same cost as their unrepairable counterparts, and can we convince people to actually repair them?
If we shared stories of the current state of e-waste recycling, we might shift attitudes. The footage of smouldering piles of old gadgets, depositing toxic fumes into the lungs of the residents of Accra (Ghana) might just get a few more repairers actively fixing their stuff.
But even if we begin to change societal attitudes, will we bother to open that cheap toothbrush to replace a failing battery, when it cost £24.99 two years ago? It had a good run; you deserve a new one…
I’m optimistic about some product categories when it comes to getting the ball-rolling, namely expensive and bulky items, but I’m also a realist: we need alternative strategies adjacent to repair. This is where we must design for disassembly.
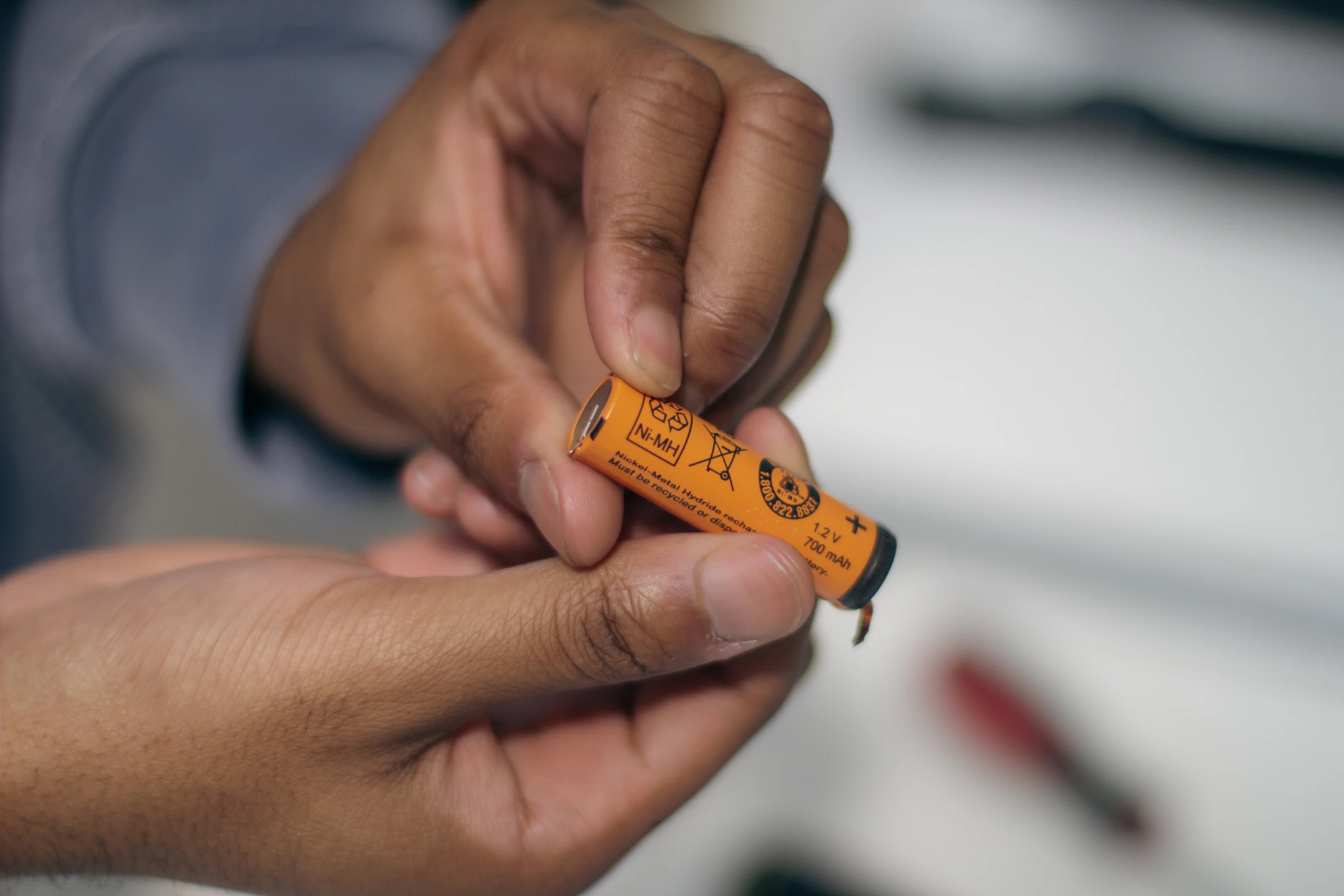
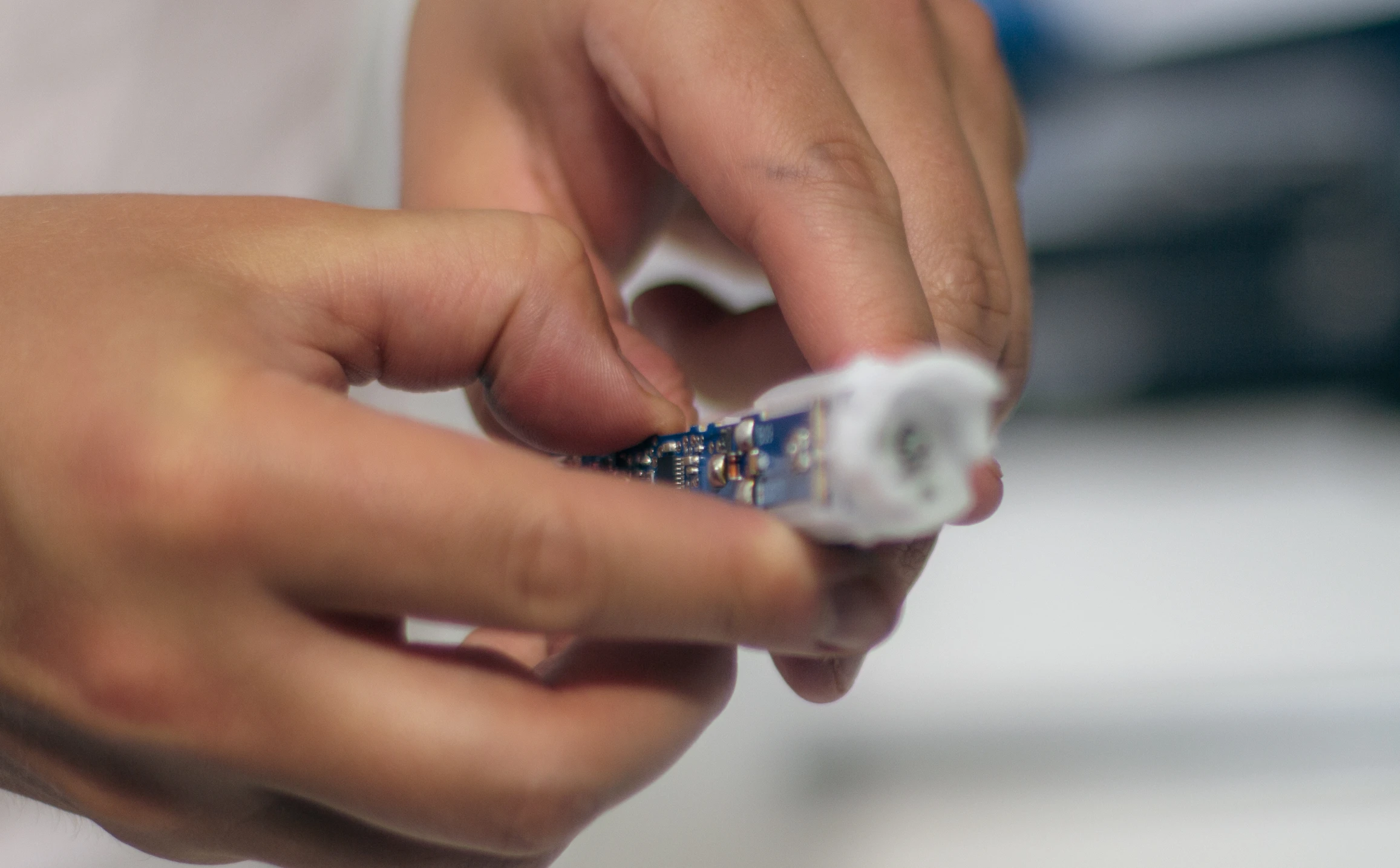
Automated Disassembly
If a product can’t be repaired and resold, then the next best option is to extract value from the components and materials inside. Design for disassembly means making this process more efficient.
Typical e-waste disassembly follows a ‘smash and burn until all that’s left is the expensive metal’ approach. Avoiding glue, using unified screws and designing simple closures are just a couple of strategies which make disassembly a breeze, compared with the usual approach.
Going a step further, we were curious to explore how efficient this process could be. What if we automated disassembly?
Like manufacturing in reverse. Apple have done this with Daisy, their disassembly robot, which they claim brings down the cost of recovering components and materials from the old iPhones they recover.
But a very expensive robot disassembling a very cheap toothbrush won’t (most likely) workout economically.
We therefore explored some different approaches to the same challenge, shown here with toothbrushes. With a little imagination, we believe the principal could work for other products.